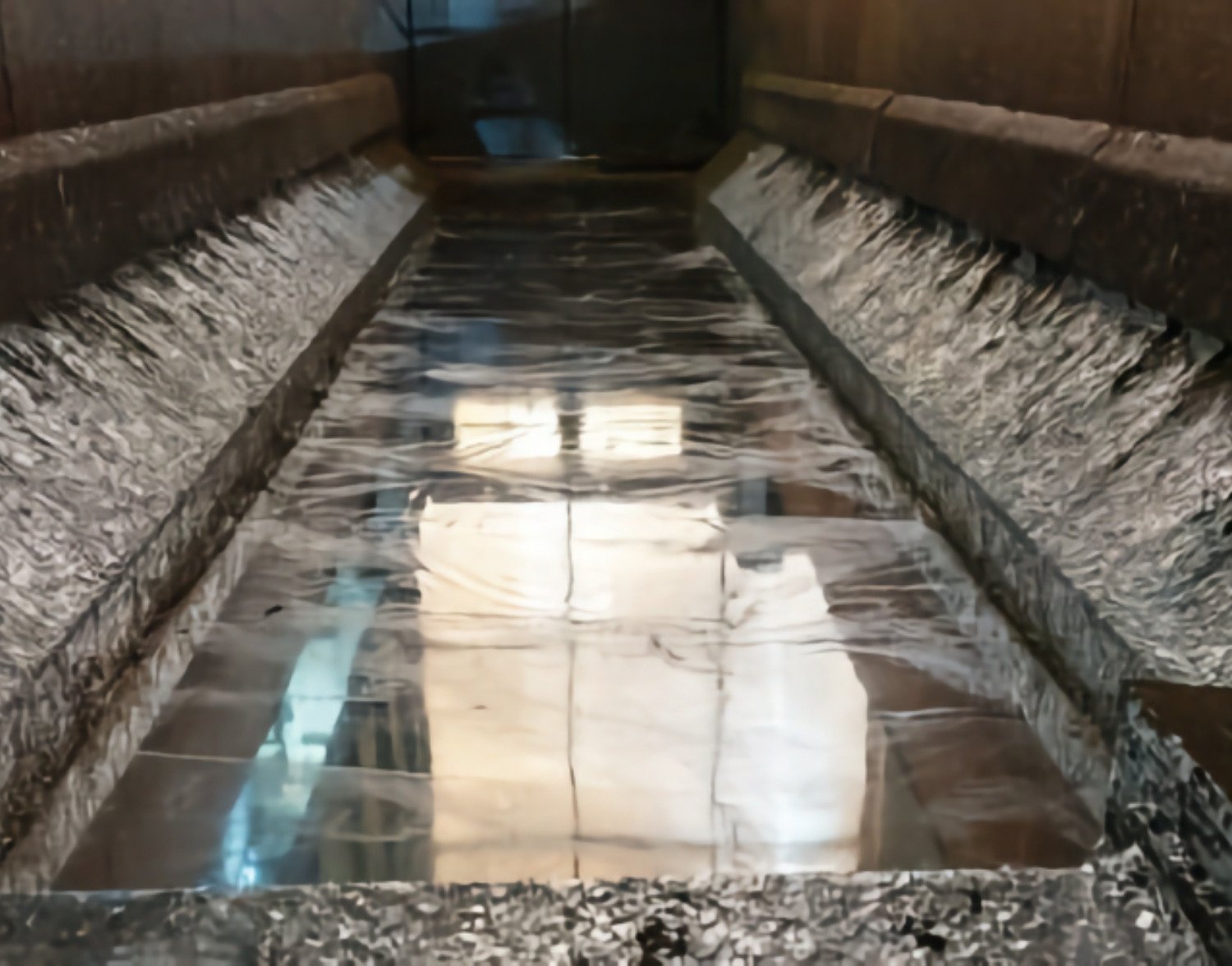
W temacie konstrukcji, montażu i konserwacji mebli, budynków, pojazdów czy szeroko pojętej infrastruktury, systemy mocujące odgrywają kluczową rolę – utrzymują ze sobą poszczególne elementy, zapewniając stabilność, funkcjonalność i trwałość przez lata. Często jednak skupiamy się głównie na doborze właściwego mocowania, bagatelizując nieco znaczenie stosowanej na nich powłoki ochronnej. Ta zaś może mieć istotny wpływ na wydajność i odporność całości na warunki atmosferyczne, korozję oraz wiele innych czynników środowiskowych.
Funkcje systemów mocujących
Systemy mocujące projektowane są tak, aby jak najlepiej spełniały konkretne funkcje, w tym:
– spajanie poszczególnych części: łączą ze sobą dwa lub więcej elementów (niejednokrotnie wykonanych z różnych materiałów), aby te nie oddzielały się od siebie,
– rozkład obciążenia: mocowania równomiernie rozkładają obciążenie, zmniejszając ryzyko uszkodzenia powierzchni lub konstrukcji,
– estetyka: w niektórych sektorach, takich jak przemysł motoryzacyjny, meblarski czy budownictwo, systemy mocujące muszą także spełniać funkcję estetyczną – tak aby nie wpływały negatywnie na wizualną stronę projektu czy gotowego produktu.
Elementy złączne wielokrotnie narażone są na rozmaite warunki atmosferyczne – takie jak wilgoć, zmiany pogody, chemikalia czy słone powietrze – które mogą powodować ich szybsze zużycie i korozję. W takich przypadkach niezbędna jest odpowiednia powłoka, aby chronić je i zachować ich estetykę, właściwości mechaniczne oraz funkcjonalność.
Znaczenie wyboru odpowiedniej powłoki
W przypadku systemów mocujących występuje kilka wariantów powłok, z których każda stosowana jest w celu zaspokojenia określonych potrzeb.
● POWŁOKA CYNKOWA
Powłoka cynkowa jest powszechnie stosowana do ochrony stalowych mocowań przed korozją powodowaną przez agresywne czynniki – nawet w środowiskach silnie utleniających.
Istnieją różne rodzaje cynkowania, a odporność korozyjna ocynkowanego elementu zależy między innymi od sposobu aplikacji powłoki, grubości nałożonego cynku oraz chropowatości powlekanego elementu.
● POWŁOKA CHROMOWA
Powłoka chromowa uszlachetnia powierzchnię danego elementu, czyniąc ją mniej podatną na atak czynników korozyjnych nawet w agresywnych środowiskach.
Utlenianie chromu powoduje tzw. pasywację powierzchni, czyli tworzenie tlenku chromu, który wzmacnia ochronę powlekanego metalu.
● POWŁOKA NIKLOWA
Powłoka niklowa, która może być wykonana chemicznie lub elektrolitycznie, zmienia cechy powierzchni obrabianego materiału, utwardzając go i uodporniając na korozję.
Proces niklowania jest obowiązkowy, jeśli na danym elemencie ma być wykonane chromowanie. Przeprowadzany jest na elementach stalowych lub mosiężnych, a także plastikowych – np. ABS pokryty wcześniej powłoką miedzianą.
● ANODOWANIE POWIERZCHNI
Jest to obróbka powierzchniowa przeprowadzana głównie na stopach aluminium, a także na tytanie i innych metalach, które nadają się do utleniania powierzchniowego (czyli hartowania).
Obróbka ta tworzy warstwę ochronną tlenku, która nadaje materiałowi wysoką odporność na korozję i agresywne czynniki zewnętrzne. Istnieje też wiele rodzajów anodowania, które umożliwiają uzyskanie estetycznie zabarwionych powierzchni.
Odporność na korozję różni się w zależności od wybranego sposobu anodowania i zależy bezpośrednio od grubości generowanego tlenku oraz chropowatości powlekanego elementu.
● ELEKTROPOLEROWANIE I PASYWACJA
Celem elektropolerowania powierzchni jest obniżenie chropowatości obrabianego elementu – tak aby cząsteczki wody lub agresywne czynniki nie mogły wnikać w porowate nierówności materiału. Ten elektrochemiczny proces w praktyce polega na usuwaniu, eliminując w ten sposób nierówności powierzchni. Dzięki późniejszej pasywacji obrabiany element ze stali nierdzewnej zyskuje wysoką odporność na korozję powierzchniową oraz wgłębną.
● POLEROWANIE – NERINOX
Polerowanie, które w przypadku stali nierdzewnej nosi nazwę NERINOX, nadaje obrabianemu elementowi większą odporność na korozję powierzchniową oraz jednolity i intensywny czarny kolor, który w zależności od wykończenia powierzchni może być błyszczący lub matowy.
Powłoka ta jest szeroko stosowana zarówno ze względów estetycznych, jak i w celu zabezpieczenia elementu przed odbijaniem światła (głównie w militariach).
● FOSFATYZACJA
To obróbka chemiczna, podczas której na powierzchni obrabianego elementu ze stali węglowej powstają kryształy fosforanów. Poprawiają one antykorozyjne właściwości stali i obniżają współczynnik tarcia, ułatwiając przesuwanie między dwoma mocowaniami. Fosfatyzacja może być cynkowa lub manganowa.
Wybór odpowiedniej powłoki ma kluczowe znaczenie dla trwałości i wydajności danego projektu. Użycie niewłaściwego rodzaju lub brak powłoki może prowadzić do szeregu problemów, takich jak:
● korozja, która może osłabić mocowanie, a w konsekwencji obniżyć jego trwałość i bezpieczeństwo,
● przedwczesne lub nagłe pęknięcia, które mogą powodować dalsze uszkodzenia i stanowić zagrożenie,
● pogorszenie estetyki, co może negatywnie wpłynąć na wizualną stronę produktu,
● dodatkowe koszty – uszkodzone lub skorodowane mocowania mogą wymagać wymiany, co prowadzi do niespodziewanych wydatków.
Wybór odpowiedniej powłoki do mocowań jest kluczowym aspektem podczas opracowywania, jak i tworzenia każdego projektu. Dobrze dobrana powłoka może poprawić odporność na korozję, trwałość i stronę estetyczną gotowego produktu, dlatego przed podjęciem decyzji bardzo istotne jest dokładne przeanalizowanie potencjalnych warunków atmosferycznych oraz wszelkich wymagań projektu.
Jeśli masz wątpliwości co do wyboru powłoki najlepiej dostosowanej do Twoich potrzeb, zapraszamy do kontaktu – nasi specjaliści służą fachową poradą.