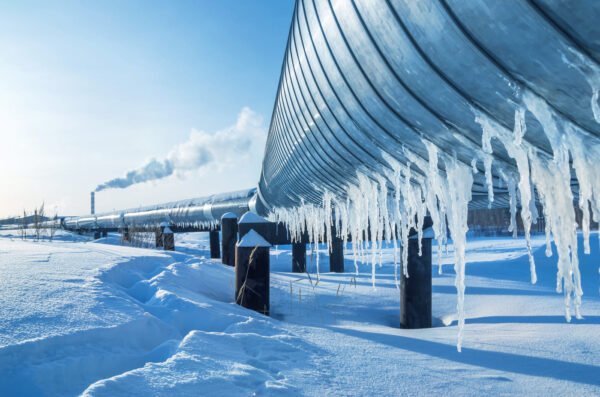
Podczas projektowania systemów mocujących istotne jest uwzględnienie warunków, w których będą one stosowane. Ogromny wpływ na wydajność i trwałość elementów mocujących ma temperatura.
Znaczenie temperatury w systemach mocujących
Narażenie na wysokie temperatury może prowadzić do rozszerzalności cieplnej, relaksacji i pełzania materiałów metalowych, co osłabia ich integralność. Jednak niskie temperatury również stanowią wyzwanie, ponieważ może zmniejszyć ciągliwość, odporność na uderzenia i stabilność strukturalną materiału. Kluczowe jest zatem wybranie takich materiałów i metod obróbki, które zapewniają im niezawodność nawet w najbardziej ekstremalnych warunkach.
Wyzwania systemów mocujących przy niskich temperaturach
Gdy temperatura spada poniżej 0°C, materiały mocujące ulegają znacznym przekształceniom, co może negatywnie wpłynąć na bezpieczeństwo i wydajność połączeń. Do głównych wyzwań, które są z tym związane, należą:
- Przejście od ciągliwości do kruchości
Wiele materiałów metalowych ulega zmianom strukturalnym, gdy są wystawione na działanie niskich temperatur. Zjawisko to, znane jako temperatura przejścia z ciągliwości do kruchości (DBTT), powoduje, że materiał traci elastyczność i staje się bardziej podatny na pękanie pod obciążeniem.
Na przykład stal węglowa klasy 2 nie nadaje się do zastosowań w temperaturach ujemnych, ponieważ staje się nadmiernie krucha. Aby zapobiec nagłym pęknięciom, konieczne jest wybranie materiałów o niskim DBTT, takich jak austenityczna stal nierdzewna o wysokiej zawartości niklu.
- Kurczliwość cieplna i utrata naprężenia wstępnego
W bardzo niskich temperaturach materiały zmniejszają swoją objętość z powodu kurczliwości cieplnej. Może to wpłynąć na stabilność łącznika, co prowadzi do:
- rozluźnienia połączenia na skutek zmniejszenia siły zacisku,
- naprężeń wewnętrznych i odkształcenia w materiałach takich jak lekkie stopy i kompozyty.
Aby temu przeciwdziałać, zaleca się stosowanie elementów złącznych o współczynniku rozszerzalności cieplnej zbliżonym do materiałów, z których wykonane są elementy mocujące, lub wybieranie rozwiązań z obróbką powierzchni i wkładkami elastycznymi, aby zrekompensować kurczenie się.
- Korozja w niskich temperaturach
Chociaż niskie temperatury spowalniają reakcje chemiczne, niektóre zjawiska korozyjne nasilają się w zimnym i wilgotnym środowisku, na przykład:
- korozja szczelinowa – jest szczególnie niebezpieczna w połączeniach z mikroszczelinami,
- kruchość wodorowa – powstaje w wyniku gromadzenia się wodoru w materiałach, co prowadzi do utraty ich wytrzymałości mechanicznej.
Aby zapewnić odporność na korozję w ekstremalnych warunkach, najlepszym rozwiązaniem są stopy niklu i wysokiej jakości stal nierdzewna, a także pasywacja i cynkowanie ogniowe, które zapewniają elementom złącznym długotrwałą ochronę.
- Zmęczenie i odporność na uderzenia w niskich temperaturach
W ekstremalnie niskich temperaturach materiały tracą również zdolność pochłaniania energii. Może to prowadzić do:
- rozwoju mikropęknięć wskutek cyklicznego obciążania i odciążania (zmęczenie materiału),
- nagłych pęknięć pod wpływem uderzeń lub wibracji.
W zastosowaniach, w których elementy złączne są narażone na wibracje lub uderzenia (np. w sektorze lotniczym, kolejowym i infrastrukturalnym), kluczowe znaczenie ma wybór materiałów o wysokiej wytrzymałości i zabezpieczonych przed zmęczeniem, takich jak stale stopowe chromowo-molibdenowe.
Elementy złączne a niskie temperatury – z jakiego materiału powinny być wykonane?
Wybór odpowiedniego materiału jest niezbędny, aby zapewnić wysoką wydajność w niskich temperaturach. Poniżej znajdziesz przykłady materiałów, które doskonale radzą sobie w takich warunkach:
Stal nierdzewna austenityczna:
- wysoka udarność i wytrzymałość mechaniczna w niskich temperaturach,
- ograniczone ryzyko przejścia materiału w stan kruchy,
- doskonała odporność na korozję.
Stopy niklu i kobaltu:
- doskonała odporność na korozję i uderzenia,
- zachowują właściwości mechaniczne do -200°C,
- stosuje się je w przemyśle lotniczym i kriogenicznych.
Tytan i stopy tytanu:
- wysoka wytrzymałość w stosunku do masy,
- odporność na zmęczenie materiału i wydajność w ekstremalnych warunkach,
- niska przewodność cieplna, przydatna w specjalistycznych zastosowaniach.
Specjalne materiały polimerowe:
- stosowane we wkładkach i tulejach termoizolacyjnych,
- wysoka odporność na wilgoć i niskie temperatury.
Zgodność z normami i wymaganiami certyfikacyjnymi
Przestrzeganie norm przemysłowych w tak wymagających warunkach jest kluczowe dla zapewnienia niezawodności systemów mocujących. Normy takie jak ASTM, DIN, ISO i EN dostarczają wytycznych dotyczących specyfikacji materiałów, właściwości mechanicznych i procedur testowych.
Wybór elementów złącznych posiadających odpowiednie certyfikaty gwarantuje spełnienie rygorystycznych kryteriów wymaganych w przypadku niskich temperatur.
Podsumowanie
Dobór elementów złącznych przeznaczonych do zastosowania w niskich temperaturach wymaga starannej oceny materiałów, metod ich obróbki, konstrukcji oraz odpowiednich certyfikatów, aby zagwarantować wytrzymałość, bezpieczeństwo i długoterminową niezawodność materiałów.
Dlatego też przed wyborem systemu mocowań należy postawić sobie kilka pytań:
- Jakie materiały będą ze sobą łączone?
- Jakie powłoki należy zastosować w elementach złącznych?
- Jaka będzie wilgotność otoczenia?
- Jaką funkcję będzie pełnił element złączny?
Odpowiedzi na te pytania powinny pomóc Ci w doborze odpowiednich elementów złącznych.
Jeśli zastanawiasz się, który produkt będzie dla Ciebie odpowiedni – zajrzy do naszej oferty https://mocujemy.pl/produkty/. W asortymencie znajdziesz elementy złączne, które sprawdzą się nawet w ekstremalnych warunkach. Skontaktuj się z nami, aby otrzymać produkt dopasowany do swoich potrzeb.